技术资料
直径4m及以上的新型水泥管模具设计制造
时间:2016-10-08|阅读:次
1. 新型大口径水泥管模具设计
整体式立式振捣水泥管模具由外模、内模、底座3个部分组成。新型大口径水泥管模具与整体式模具不同点在于将外模分为上、中、下3个部分。整套模具结构主要包括:底座、底模、中模、顶模以及内模。
管材精度要求最高的地方是承口和插口工作面直径,这主要取决于水泥管模具中外模的承口和插口部分。传统模具的外模一般采用两半模,其插口和承口部分均由两半组成,这不仅对保证管材接口工作圆度是不利的,并且模具在使用过程中焊接应力释放以及反复拆装过程中的疲劳受力,均会引起模具变形,致使接口精度逐渐超标,直至模具报废。但如果为了减少变形而一味提高半模的刚度也是不可取的,这会带来拆模困难,需使用更大的力来拆模,不仅损伤模具,甚至还会损坏管材接口。据此,采用了如下的改进设计方法。
1)将上模设计成内外2层,外层(插口定位模)为整圆,内层(插口定型模)为两半式。内层两半模采用合理的弹性变形量,提高模具抵抗反复拆装过程中疲劳变形的能力,延长模具的使用寿命。同时,由于内层模具有一定的容许变形量,故模具脱模时十分便捷。外层模具用整体浇钢件,以提高模具刚度和强度,保证上模整体精度。将整体模与两半模结合,优势互补,整体模具,分体拆装,既保证模具精度,又便于拆装,反复使用也不易变形。
2)中模采用2个半模组成,两端采用螺栓连接,模具上下都有装配限位机构。中模分别与上模和底模连接,由于上下均为整体结构,故更容易保证底模的圆度。此外,中模上的吊耳与工作平台做了集成,从而使结构简单化和通用化,节省了材料,降低了成本。由于管节外直径达到4640mm,故中模在设计上应考虑到脱模时的吸附作用,在中模加筋板的设置上,通过与科研院校产研结合,经过计算后合理布置加筋板的厚度和高度,使得中模具有弹性变形的能力。
3)下模是传统模具的底模与外模下部的组合,全部设计成整体式。底模的零件采用浇铸的工艺,使得零件的精度达到比较高的水平。零件与零件采用了精准定位系统,提高了生产时零件的装配精度。
4)对传统内模进行结构上的优化。内模采用无缝钢管和低合金高强度16Mn钢板焊接而成。而半内模采用铰链连接,使得在内模拉动时方便可靠。内模插板采用螺栓顶住插板边使得插板往外移动,中间横梁结构中螺栓是插板在拆卸时的辅助拆卸装置。该装置的优点在于结构简单可靠,使用方便易操作。
1.1 底座设计
底座结构主要以圆形工字型钢为支架,其上是一块圆环钢板和混凝土管承口钢圈定位件。由于生产管件的高精度要求,故对圆环钢板以及混凝土管承口钢圈定位件的加工精度要求很高,其受力后的变形量也必须受到严格的控制。设计结构如图1所示。
整体式立式振捣水泥管模具由外模、内模、底座3个部分组成。新型大口径水泥管模具与整体式模具不同点在于将外模分为上、中、下3个部分。整套模具结构主要包括:底座、底模、中模、顶模以及内模。
管材精度要求最高的地方是承口和插口工作面直径,这主要取决于水泥管模具中外模的承口和插口部分。传统模具的外模一般采用两半模,其插口和承口部分均由两半组成,这不仅对保证管材接口工作圆度是不利的,并且模具在使用过程中焊接应力释放以及反复拆装过程中的疲劳受力,均会引起模具变形,致使接口精度逐渐超标,直至模具报废。但如果为了减少变形而一味提高半模的刚度也是不可取的,这会带来拆模困难,需使用更大的力来拆模,不仅损伤模具,甚至还会损坏管材接口。据此,采用了如下的改进设计方法。
1)将上模设计成内外2层,外层(插口定位模)为整圆,内层(插口定型模)为两半式。内层两半模采用合理的弹性变形量,提高模具抵抗反复拆装过程中疲劳变形的能力,延长模具的使用寿命。同时,由于内层模具有一定的容许变形量,故模具脱模时十分便捷。外层模具用整体浇钢件,以提高模具刚度和强度,保证上模整体精度。将整体模与两半模结合,优势互补,整体模具,分体拆装,既保证模具精度,又便于拆装,反复使用也不易变形。
2)中模采用2个半模组成,两端采用螺栓连接,模具上下都有装配限位机构。中模分别与上模和底模连接,由于上下均为整体结构,故更容易保证底模的圆度。此外,中模上的吊耳与工作平台做了集成,从而使结构简单化和通用化,节省了材料,降低了成本。由于管节外直径达到4640mm,故中模在设计上应考虑到脱模时的吸附作用,在中模加筋板的设置上,通过与科研院校产研结合,经过计算后合理布置加筋板的厚度和高度,使得中模具有弹性变形的能力。
3)下模是传统模具的底模与外模下部的组合,全部设计成整体式。底模的零件采用浇铸的工艺,使得零件的精度达到比较高的水平。零件与零件采用了精准定位系统,提高了生产时零件的装配精度。
4)对传统内模进行结构上的优化。内模采用无缝钢管和低合金高强度16Mn钢板焊接而成。而半内模采用铰链连接,使得在内模拉动时方便可靠。内模插板采用螺栓顶住插板边使得插板往外移动,中间横梁结构中螺栓是插板在拆卸时的辅助拆卸装置。该装置的优点在于结构简单可靠,使用方便易操作。
1.1 底座设计
底座结构主要以圆形工字型钢为支架,其上是一块圆环钢板和混凝土管承口钢圈定位件。由于生产管件的高精度要求,故对圆环钢板以及混凝土管承口钢圈定位件的加工精度要求很高,其受力后的变形量也必须受到严格的控制。设计结构如图1所示。
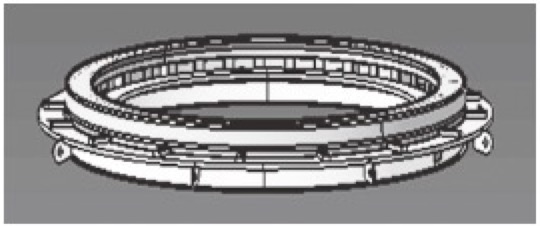
图1 底座设计结构示意
底座与地面接触件承受整个模具以及行走机构和混凝土管的质量。由于工字型钢具有较好的抗压强度,且已标准化,能减少设计成本和加工成本,故选用工字型钢为底座的支架。钢板为铸钢件,主要作用是作模具的安装平台。该结构件为铸钢件,主要作用是定位承口钢圈,采用2个定位销来定位其在圆形钢板上的位置。
1.2 底模设计
底模主要是用来保证插口钢圈的圆度误差,同时底模的精度直接影响到中模的定位,底模的结构如图2所示。
1.2 底模设计
底模主要是用来保证插口钢圈的圆度误差,同时底模的精度直接影响到中模的定位,底模的结构如图2所示。
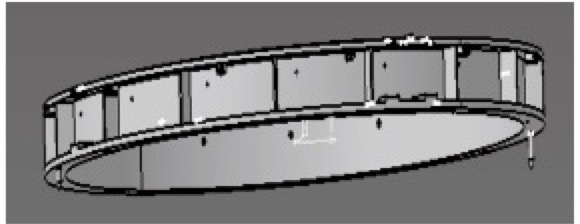
图2 底模结构
使用2根定位销来限定底模在底座上的位置。其中一根定位销较长,安装模具时,先将较长的定位销插入底座的一个定位孔,然后再将另一根定位销插入定位孔中,这样定位较精确且更便于操作。底模圆周上有16个定位孔,用于定位承口钢圈。具体方法是待钢圈放入模具后,将16根螺栓旋入定位孔,根据钢圈外壁到模具内壁间的距离来调节对应螺栓,通过反复的操作来保证钢圈的圆度误差。
底模下板面设计有8个千斤顶安装座,用于安装脱模用千斤顶装置。
底模上板面为一凸起面结构,目的是为了方便精确定位中模。当放入中模时,使中模的下端法兰面与该面重合,即可实现中模的精确定位,如图3(a)所示。注浆时考虑混凝土浆渗漏,在底模与中模结合部位增加密封装置,设计采用2道密封。为了使每次拆卸模具时密封条不至于被拉出,密封圈采用燕尾槽结构,如图3(b)所示。底模与中模使用12个如图3(c)所示结构连接。
托板机构主要是起到脱模时拖住混凝土管、防止掉落的作用,其结构如图4(a)所示。主要结构由托板、板手、螺栓、弹簧垫圈以及板手与托板间周向定位的平键组成。板手与钢模的装配关系如图4(b)所示。
底模下板面设计有8个千斤顶安装座,用于安装脱模用千斤顶装置。
底模上板面为一凸起面结构,目的是为了方便精确定位中模。当放入中模时,使中模的下端法兰面与该面重合,即可实现中模的精确定位,如图3(a)所示。注浆时考虑混凝土浆渗漏,在底模与中模结合部位增加密封装置,设计采用2道密封。为了使每次拆卸模具时密封条不至于被拉出,密封圈采用燕尾槽结构,如图3(b)所示。底模与中模使用12个如图3(c)所示结构连接。
托板机构主要是起到脱模时拖住混凝土管、防止掉落的作用,其结构如图4(a)所示。主要结构由托板、板手、螺栓、弹簧垫圈以及板手与托板间周向定位的平键组成。板手与钢模的装配关系如图4(b)所示。
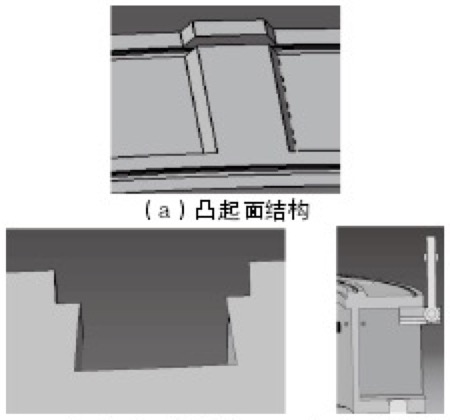
图3 底模结构局部放大示意
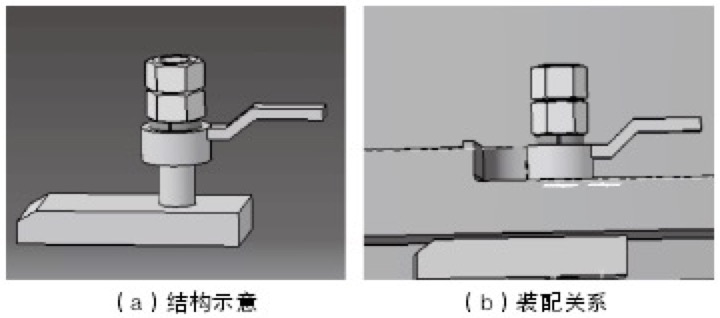
图4 拖板机构
1.3 中模设计
中模的外围结构大体上采用以往的肋板加强圆形模壁结构的设计形式,如图5所示。与以往小直径水泥管整体式模具不同,该模具制造的混凝土管直径达4m以上,总质量很大,因此为了便于施工时的搬运及翻转,需要在混凝土重心位置的壁面上设置吊装孔。由于施工时需要翻转混凝土管,将混凝土从竖直位置放平,故吊装孔设计成方形。吊装孔的加入使得以往的模具整体式结构设计不再适用,必须采用分开式结构。通过对比各种设计方案,最终采用两半对开式结构。结构设计时要先保证模具精度,与底模的定位必须要简单、安全、可靠,工人在安装时要省时、省力。中模与底模、顶模的定位结构如图6所示。为了保证圆柱度和平行度,模具采用锥面定位。由于中模结构为两半模,故必然要考虑到两半模间的定位。设计采用销定位,在半模的结合面上使用2个定位销。为了降低整个模具及装料装置的高度,项目部将供工作人员行走的围栏装置支撑结构设计在中模上,如图5所示模外壁上的吊钩。由于采用两对模结构设计形式,故必然要考虑到对模连接处的密封。同上面的密封形式一样,在连接处采用燕尾槽式的结构,密封条形状为齿形。
1.4 顶模设计
根据水泥管设计要求,顶模中要预埋钢带,因此顶模不能做成整圆式的。如若同中模一样做成2个半环式结构,则其定位带来的误差必须导致模具精度的降低,且按此设计将必然给模具的制造带来更高的要求,最终增加了模具的制造成本。因此项目部采用具有独创性的设计结构,如图7所示。
中模的外围结构大体上采用以往的肋板加强圆形模壁结构的设计形式,如图5所示。与以往小直径水泥管整体式模具不同,该模具制造的混凝土管直径达4m以上,总质量很大,因此为了便于施工时的搬运及翻转,需要在混凝土重心位置的壁面上设置吊装孔。由于施工时需要翻转混凝土管,将混凝土从竖直位置放平,故吊装孔设计成方形。吊装孔的加入使得以往的模具整体式结构设计不再适用,必须采用分开式结构。通过对比各种设计方案,最终采用两半对开式结构。结构设计时要先保证模具精度,与底模的定位必须要简单、安全、可靠,工人在安装时要省时、省力。中模与底模、顶模的定位结构如图6所示。为了保证圆柱度和平行度,模具采用锥面定位。由于中模结构为两半模,故必然要考虑到两半模间的定位。设计采用销定位,在半模的结合面上使用2个定位销。为了降低整个模具及装料装置的高度,项目部将供工作人员行走的围栏装置支撑结构设计在中模上,如图5所示模外壁上的吊钩。由于采用两对模结构设计形式,故必然要考虑到对模连接处的密封。同上面的密封形式一样,在连接处采用燕尾槽式的结构,密封条形状为齿形。
1.4 顶模设计
根据水泥管设计要求,顶模中要预埋钢带,因此顶模不能做成整圆式的。如若同中模一样做成2个半环式结构,则其定位带来的误差必须导致模具精度的降低,且按此设计将必然给模具的制造带来更高的要求,最终增加了模具的制造成本。因此项目部采用具有独创性的设计结构,如图7所示。
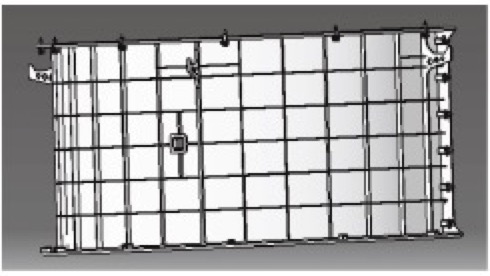
图5 中模结构
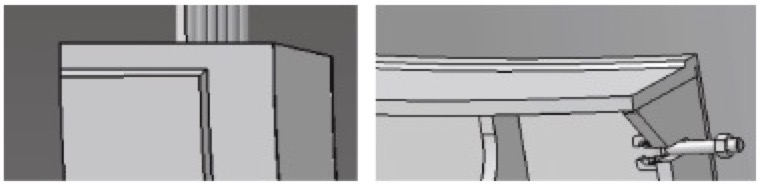
图6 中模与底模、顶模定位结构
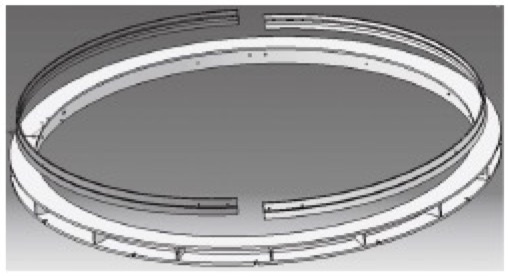
图7 顶模结构
顶模主要由3部分组成,即2个半圆形刚性模和1个圆形铸钢件。半圆形模与铸钢件间采用圆锥面定位。如此设计的优点在于:既可以实现预存钢带的功能,又具有整体式模具定位精度高的优势。组装时,先将预存钢带放入两半环内槽内,再压入圆形铸钢件中。为防止刚性模调运时掉落,在铸钢件壁上设有弹性卡销,在与之对应的刚性模上开槽,待装配好后将弹性卡销插入其中即可实现预防功能。由于钢与钢间存在摩擦等,可能使装配好的模具无法分离,故在刚性模上装有内六角螺钉,在无法脱模时用板手向内旋动螺钉便可脱模。顶模与中模使用2根长短不同的定位销进行粗定位;与中模上的法兰面类似,顶模采用与之相匹配的凹面结构作为定位面结构。注浆过程会发生漏浆,因此要设计密封结构。为防止密封条在重复拆装时掉落,密封槽也采用同中模与底模密封一样的燕尾槽结构。
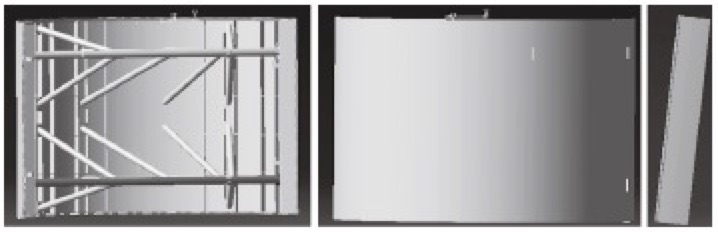
图8 内模主要组成部分
1.5 内模设计
参照目前小型水泥管模具设计,内模主要由3个部分组成:2个主半模和1个楔形块。其结构如图8所示。内模内部采用圆钢管作为支撑架,在保证相同强度的情况下,可以大大降低模具的总质量。为了使模具结合更紧密,将内模的两主半模的连接结构移至内部,大大增加了内模连接处的密封性能。
2. 新型大口径水泥管模具整体疲劳分析
由于模具在工作时内部需通入高温蒸汽,因此要对模具整体进行热疲劳分析。首先在模型受到100℃高温时模拟仿真钢模整体热应力和疲劳情况。使用Msc.Fatigue软件,采用S-N方法进行疲劳分析。计算结果如图9所示,分析结构表明,该设计符合使用寿命要求。
参照目前小型水泥管模具设计,内模主要由3个部分组成:2个主半模和1个楔形块。其结构如图8所示。内模内部采用圆钢管作为支撑架,在保证相同强度的情况下,可以大大降低模具的总质量。为了使模具结合更紧密,将内模的两主半模的连接结构移至内部,大大增加了内模连接处的密封性能。
2. 新型大口径水泥管模具整体疲劳分析
由于模具在工作时内部需通入高温蒸汽,因此要对模具整体进行热疲劳分析。首先在模型受到100℃高温时模拟仿真钢模整体热应力和疲劳情况。使用Msc.Fatigue软件,采用S-N方法进行疲劳分析。计算结果如图9所示,分析结构表明,该设计符合使用寿命要求。
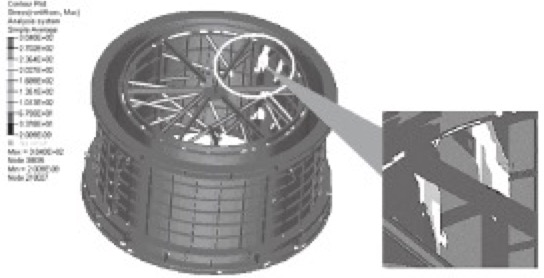
图9 有限元计算结果
3. 结语
本文针对超大口径水泥管模具进行了设计,本设计在以往设计的基础上,将钢模结构分为了底模、中模、顶模、内模以及底座。采用分开式结构降低了模具的精度,为了提高模具精度,设计中大量采用了各种定位措施,如锥面的应用、定位销的应用等。为防止混凝土泄漏,对钢模的密封措施进行了重新设计。同时引入了轻量化设计的理念,在保证模具精度的前提下,降低了钢模自身的质量,并对减重后钢模进行有限元寿命分析,确保钢模满足施工要求。
本文针对超大口径水泥管模具进行了设计,本设计在以往设计的基础上,将钢模结构分为了底模、中模、顶模、内模以及底座。采用分开式结构降低了模具的精度,为了提高模具精度,设计中大量采用了各种定位措施,如锥面的应用、定位销的应用等。为防止混凝土泄漏,对钢模的密封措施进行了重新设计。同时引入了轻量化设计的理念,在保证模具精度的前提下,降低了钢模自身的质量,并对减重后钢模进行有限元寿命分析,确保钢模满足施工要求。