技术资料
横腹杆式预应力砼支柱关键工序作业指导书
时间:2015-01-30|阅读:次
第一章 砼搅拌
1、技术要求
1.1 搅拌砼用各种材料应符合GB175;GB/T14684、GB/T14685;GB8076及JGJ63标准要求。
1.2 各种计量秤应示值准确,性能良好,且在检定周期内使用。
1.3 原材料称量误差:粗、细骨料不大于3%;其余不大于2%。
1.4 严格按配合比称料,不得随意更改,用水量可以少许调整。
1.5 砼干稀程度用增实因数控制,其增实因数控制在1.20~1.30之间。也可以用坍落度来控制,其数值在5~10mm之内。
1.6 砼强度等级为C60。
2、操作方法
2.1 接通电源,使计算机等仪器、设备处于工作状态。
2.2 检验各种仪器、设备示值情况,是否准确可靠。
2.3 启动砼搅拌机进行空运转,检测各部零件是否为好用。同时砼输送小车应在接料位置上。
2.4 根据生产支柱品种、型号、数量从计算机输出砼配料方案,并进行确定。
2.5 应根据支柱生产进度决定投料:投料时,先下砂子、水泥和80%的水,搅拌60s,再下碎石搅拌10s,后下减水剂及余下的水,各种材料投完后,净搅拌时间不少于90s。用肉眼观察砼拌合物的干稀程度,可作出必要的调整,认为无误方可放料。
2.6 放料前必须检查砼输送车位置,以免将砼拌合物下到地下。下料时用压缩空气打开搅拌机下料口进行下料,用小铲清整下料斗,以免硬化影响使用。
2.7 每班结束搅拌时,必须对搅拌机、运输车及下料斗进行清洗。
2.8 搅拌人员负责将搅拌记录打印出来,并签名。
1.1 搅拌砼用各种材料应符合GB175;GB/T14684、GB/T14685;GB8076及JGJ63标准要求。
1.2 各种计量秤应示值准确,性能良好,且在检定周期内使用。
1.3 原材料称量误差:粗、细骨料不大于3%;其余不大于2%。
1.4 严格按配合比称料,不得随意更改,用水量可以少许调整。
1.5 砼干稀程度用增实因数控制,其增实因数控制在1.20~1.30之间。也可以用坍落度来控制,其数值在5~10mm之内。
1.6 砼强度等级为C60。
2、操作方法
2.1 接通电源,使计算机等仪器、设备处于工作状态。
2.2 检验各种仪器、设备示值情况,是否准确可靠。
2.3 启动砼搅拌机进行空运转,检测各部零件是否为好用。同时砼输送小车应在接料位置上。
2.4 根据生产支柱品种、型号、数量从计算机输出砼配料方案,并进行确定。
2.5 应根据支柱生产进度决定投料:投料时,先下砂子、水泥和80%的水,搅拌60s,再下碎石搅拌10s,后下减水剂及余下的水,各种材料投完后,净搅拌时间不少于90s。用肉眼观察砼拌合物的干稀程度,可作出必要的调整,认为无误方可放料。
2.6 放料前必须检查砼输送车位置,以免将砼拌合物下到地下。下料时用压缩空气打开搅拌机下料口进行下料,用小铲清整下料斗,以免硬化影响使用。
2.7 每班结束搅拌时,必须对搅拌机、运输车及下料斗进行清洗。
2.8 搅拌人员负责将搅拌记录打印出来,并签名。
第二章 钢丝预应力
1、标准要求
1.1 所用预应主筋应符合GB/T5223《预应力砼用钢丝》。
1.2 在编组及张拉时应保证预应力钢丝受力均匀。
1.3 主筋下料长度误差不大于2.0mm,镦头直径应在Ф7.0~Ф7.5之间,镦头高度为4.0~4.5mm。
1.4 各种型号支柱下料长度、根数、张拉值。
1.5 各种型号支柱配筋图。
1.6 测力用力压表量程0~40MPa;精度等级1.0,张拉用千斤机采用YL600型,活塞有效面积为162.58cm2,如用其它型号千斤顶张拉时,表压力另定。各种计量仪器均按规定进行检定。
1.7 千斤顶、油泵及管路不得漏油,千斤顶摩擦系数不大于1.03,如发现压力表抬钟运转不灵活或不回零位,应及时更换新表。
2、操作方法
2.1 开始张拉时支柱模型应处于合模状态,全部螺帽紧固完毕,确认规格型号、钢丝根数、设定张拉限值。
2.2 开动油泵,使之空运转30s,后测试千斤顶拉伸是否灵活有效。
2.3 联接张拉杆,注意联搪头上标志。双线必须对准,方可使用。调整张拉中心,如张拉中心不对,可用手拉葫芦调整。
2.4 关闭回油阀,使千斤顶拉伸。此时另一个阀门必须打开。当拉至4MPa时暂停张拉,用纤子或锤子将锚块靠严。
2.5 当拉到设定值后,停1min,并紧螺帽;当时间达1min后再拉至设定值,用手锤敲紧螺帽。
2.6 张拉钢筋时模型两端严禁站人或有人通过,厂应采取防护板,以免断丝飞出伤人。
2.7 打开回油阀,关闭另一油阀使千斤顶活塞退出,将联接头旋转90。卸下。
2.8 张拉人员认真填写张拉记录,并签名,保存。
1.1 所用预应主筋应符合GB/T5223《预应力砼用钢丝》。
1.2 在编组及张拉时应保证预应力钢丝受力均匀。
1.3 主筋下料长度误差不大于2.0mm,镦头直径应在Ф7.0~Ф7.5之间,镦头高度为4.0~4.5mm。
1.4 各种型号支柱下料长度、根数、张拉值。
编号 | 型号 | 下料长度(mm) | 根数 | 张拉值(MPa) |
1 | H60/8.7+3.0 | 12020 | 20 | 21.0 |
H78/8.7+3.0 | 28 | 29.8 | ||
H93/8.7+3.0 | 26 | 27.6 | ||
2 | H60/9.2+3.0 | 12520 | 20 | 21.0 |
H78/9.2+3.0 | 28 | 29.8 | ||
H93/9.2+3.0 | 26 | 27.6 | ||
3 | H170/12+3.5 | 15800 | 38 |
上:14.9 下:25.6 |
1.5 各种型号支柱配筋图。
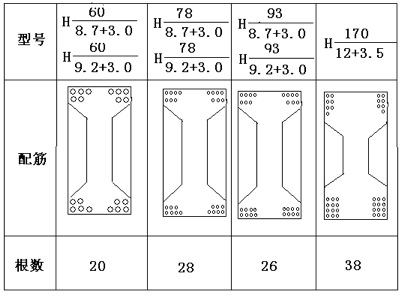
1.6 测力用力压表量程0~40MPa;精度等级1.0,张拉用千斤机采用YL600型,活塞有效面积为162.58cm2,如用其它型号千斤顶张拉时,表压力另定。各种计量仪器均按规定进行检定。
1.7 千斤顶、油泵及管路不得漏油,千斤顶摩擦系数不大于1.03,如发现压力表抬钟运转不灵活或不回零位,应及时更换新表。
2、操作方法
2.1 开始张拉时支柱模型应处于合模状态,全部螺帽紧固完毕,确认规格型号、钢丝根数、设定张拉限值。
2.2 开动油泵,使之空运转30s,后测试千斤顶拉伸是否灵活有效。
2.3 联接张拉杆,注意联搪头上标志。双线必须对准,方可使用。调整张拉中心,如张拉中心不对,可用手拉葫芦调整。
2.4 关闭回油阀,使千斤顶拉伸。此时另一个阀门必须打开。当拉至4MPa时暂停张拉,用纤子或锤子将锚块靠严。
2.5 当拉到设定值后,停1min,并紧螺帽;当时间达1min后再拉至设定值,用手锤敲紧螺帽。
2.6 张拉钢筋时模型两端严禁站人或有人通过,厂应采取防护板,以免断丝飞出伤人。
2.7 打开回油阀,关闭另一油阀使千斤顶活塞退出,将联接头旋转90。卸下。
2.8 张拉人员认真填写张拉记录,并签名,保存。
第三章 振动成型
1 技术要求
1.1 灌注砼前,应检查各种预埋件是否安放齐全、牢固,预留孔位置有无偏差。检验构造筋是否贴在模型上。
1.2 灌注砼时,要采用三次下料法,每次下料量控制在总量的三分之一左右。第一次下料完成后即可开始振动。
1.3 振动时间不少于12min,振动效果以砼表面不再下沉、无气泡排出为度。
1.4 振动过程中要检查合模螺母有无松动、压管架是否松动、有无漏浆现象。如有上述问题应停止振动,经处于是后再振动。
1.5 振动结束后,应轻吊、轻落,一般静停30min后抹平压光。
2、操作方法
2.1 砼灌注车装料前应使风部湿润,各部零件动转正常,螺旋输送机处于良好工作状态。
2.2 开动灌注车向模型内注料,操作司机应边下料边注意小车行走,按钢模形状下料,做到下料均匀,无遗漏。
2.3 开动振动台,(计时)振动3min,开始第二次下料,此时可以边下料边振动。第三次下料时应注意下料量,不可下料过多。
2.4 如发现下料过量,可以人工平灰。同时用抹子边振边抹,填满砼至模型标定位置。
2.5 检查预留孔压管架螺母是否松动,产生移位如有上述现象发生,及时处理,可再开振动台振一下。
2.6 如有气泡排除困难,可用纤子进行插捣或用Ф30mm振动棒附助振动。
2.7 当振动结束后,卸下压管架,操作工对支柱上表面进行抹平,对模型两端漏浆处进行清理,防止砼硬化后影响切割主筋。
2.8 及时吊运到位。当支柱表面收浆后,用压子将支柱表面压光,此项工作也在养护窑内完成。
1.1 灌注砼前,应检查各种预埋件是否安放齐全、牢固,预留孔位置有无偏差。检验构造筋是否贴在模型上。
1.2 灌注砼时,要采用三次下料法,每次下料量控制在总量的三分之一左右。第一次下料完成后即可开始振动。
1.3 振动时间不少于12min,振动效果以砼表面不再下沉、无气泡排出为度。
1.4 振动过程中要检查合模螺母有无松动、压管架是否松动、有无漏浆现象。如有上述问题应停止振动,经处于是后再振动。
1.5 振动结束后,应轻吊、轻落,一般静停30min后抹平压光。
2、操作方法
2.1 砼灌注车装料前应使风部湿润,各部零件动转正常,螺旋输送机处于良好工作状态。
2.2 开动灌注车向模型内注料,操作司机应边下料边注意小车行走,按钢模形状下料,做到下料均匀,无遗漏。
2.3 开动振动台,(计时)振动3min,开始第二次下料,此时可以边下料边振动。第三次下料时应注意下料量,不可下料过多。
2.4 如发现下料过量,可以人工平灰。同时用抹子边振边抹,填满砼至模型标定位置。
2.5 检查预留孔压管架螺母是否松动,产生移位如有上述现象发生,及时处理,可再开振动台振一下。
2.6 如有气泡排除困难,可用纤子进行插捣或用Ф30mm振动棒附助振动。
2.7 当振动结束后,卸下压管架,操作工对支柱上表面进行抹平,对模型两端漏浆处进行清理,防止砼硬化后影响切割主筋。
2.8 及时吊运到位。当支柱表面收浆后,用压子将支柱表面压光,此项工作也在养护窑内完成。
第四章 绑扎钢筋
1、技术要求
1.1 所用钢筋应符合GB/T701-1997;GB/T343-1994及GB1499标准三规定。
1.2 各种骨架筋、网片、构造筋,其规格、数量、尺寸增应满足图纸要求。
1.3 各种钢筋按图纸设计位置安放,误差不大于10mm。
1.4 各种钢筋均应焊接牢固、焊点齐全,按一定顺序堆放,不得混堆;钢筋名称、编号应挂标签标识。
1.5 钢筋绑扎时用双股22#铁丝绑扎牢固,钢筋交叉点必须绑扎,绑扎线头不应向外伸出。
2、操作方法
2.1 将预应力主筋按先小端后大端的顺序,挂在张拉头上及大端承力板的槽口内,挂筋时应确认整但钢筋是否平行。可以用力拉动一下边上两根钢筋来确认。确认后再装入槽口内。
2.2 将小端张拉螺母拧紧至张拉杆端头120mm处,将手拉葫芦拉紧,以钢筋被拉直为度。一般拉力在20KN左右。
2.3 先将上、下两层主筋用Ф6.0mm钢棒分开,形成有利于钢筋网片绑扎的局面。
2.4 先放入K1及K6网片,后上③、④号箍筋,再放K3及K5至主筋两层之间,最后放K2和K4。构造筋按K3-K19依次安放。
2.5 绑扎时按图纸进行,边绑扎边用钢卷尺测量其绑扎位置是否正确。
2.6 每模型上应设6处限止钩,防止夹筋。 型号支柱,用60个箍筋来防止主筋夹在钢模内。
2.7 发现钢筋网片制作不好,尺寸有问题要及时处理,合格后再绑扎,否则应弃掉。
2.8 钢筋绑扎结束后,须将模型内存放钢筋,绑线及杂物清理干净。将多余的钢筋剪掉,钢棒拔出。
2.9 用木棒将钢筋敲至规定的位置,以免合模时夹在芯孔内或露筋。
1.1 所用钢筋应符合GB/T701-1997;GB/T343-1994及GB1499标准三规定。
1.2 各种骨架筋、网片、构造筋,其规格、数量、尺寸增应满足图纸要求。
1.3 各种钢筋按图纸设计位置安放,误差不大于10mm。
1.4 各种钢筋均应焊接牢固、焊点齐全,按一定顺序堆放,不得混堆;钢筋名称、编号应挂标签标识。
1.5 钢筋绑扎时用双股22#铁丝绑扎牢固,钢筋交叉点必须绑扎,绑扎线头不应向外伸出。
2、操作方法
2.1 将预应力主筋按先小端后大端的顺序,挂在张拉头上及大端承力板的槽口内,挂筋时应确认整但钢筋是否平行。可以用力拉动一下边上两根钢筋来确认。确认后再装入槽口内。
2.2 将小端张拉螺母拧紧至张拉杆端头120mm处,将手拉葫芦拉紧,以钢筋被拉直为度。一般拉力在20KN左右。
2.3 先将上、下两层主筋用Ф6.0mm钢棒分开,形成有利于钢筋网片绑扎的局面。
2.4 先放入K1及K6网片,后上③、④号箍筋,再放K3及K5至主筋两层之间,最后放K2和K4。构造筋按K3-K19依次安放。
2.5 绑扎时按图纸进行,边绑扎边用钢卷尺测量其绑扎位置是否正确。
2.6 每模型上应设6处限止钩,防止夹筋。 型号支柱,用60个箍筋来防止主筋夹在钢模内。
2.7 发现钢筋网片制作不好,尺寸有问题要及时处理,合格后再绑扎,否则应弃掉。
2.8 钢筋绑扎结束后,须将模型内存放钢筋,绑线及杂物清理干净。将多余的钢筋剪掉,钢棒拔出。
2.9 用木棒将钢筋敲至规定的位置,以免合模时夹在芯孔内或露筋。
第五章 支柱养护
1、技术要求
1.1 养护制度2-2-6-1。即静停时不于2h;升温时间不少于2h;恒温时间不少于6h,要有一定的降温时间,恒温温度不超过80℃。
1.2 养护用蒸汽,养护窑应窑闭,并安装热介质定向循环装置,使窑内各点温度均匀,确保支柱养护质量。
1.3 养护窑易采用计算机控制,各阶段的温度误差不大于2℃,并有自动调解温度,时间及记录打印功能。
1.4 支柱出窑后用60*80mm方木垫好。在成品堆场内保持湿润,浇水养护14天后方可结束养护。
2、操作方法
2.1 养护前应确定:窑号、产品名称、规格型号、数量、盖窑时间,并作记录。
2.2 打开计算机设定养护制度。并与锅炉房人员联系送气,观察窑盖是否盖严,有无漏气可能。有问题及时处理。
2.3 按设定程序进行养护,同时应认真填写养护记录。
2.4 当完成养护程序后,测温人员应及时通知有关人员,进行下一步工作。
2.5 揭开窑盖小窗口,取出砼试块,进行强度检验。当试块达到标准要求时,方可揭窑。
2.6 测温人员负责填写养护记录并打印养护资料并在记录上签名。
2.7 支柱运至堆场后用自来水浇上表面,并用蓬布或塑料布覆盖用以保温。
1.1 养护制度2-2-6-1。即静停时不于2h;升温时间不少于2h;恒温时间不少于6h,要有一定的降温时间,恒温温度不超过80℃。
1.2 养护用蒸汽,养护窑应窑闭,并安装热介质定向循环装置,使窑内各点温度均匀,确保支柱养护质量。
1.3 养护窑易采用计算机控制,各阶段的温度误差不大于2℃,并有自动调解温度,时间及记录打印功能。
1.4 支柱出窑后用60*80mm方木垫好。在成品堆场内保持湿润,浇水养护14天后方可结束养护。
2、操作方法
2.1 养护前应确定:窑号、产品名称、规格型号、数量、盖窑时间,并作记录。
2.2 打开计算机设定养护制度。并与锅炉房人员联系送气,观察窑盖是否盖严,有无漏气可能。有问题及时处理。
2.3 按设定程序进行养护,同时应认真填写养护记录。
2.4 当完成养护程序后,测温人员应及时通知有关人员,进行下一步工作。
2.5 揭开窑盖小窗口,取出砼试块,进行强度检验。当试块达到标准要求时,方可揭窑。
2.6 测温人员负责填写养护记录并打印养护资料并在记录上签名。
2.7 支柱运至堆场后用自来水浇上表面,并用蓬布或塑料布覆盖用以保温。