技术资料
水泥制管机械预制管涵的质量管理措施
时间:2015-03-30|阅读:次
我国生产水泥管的企业绝大多数属于小微企业,技术水平低、生产装备落后,对生产工艺和成品检验把关不严,很难保证水泥管的产品质量。针对这种情况,我司为帮助水泥管生产企业产品达到《混凝土和钢筋混凝土排水管》国家标准要求,提出以下改进措施。
1. 原材料控制
根据水泥管生产的特殊性,砂、石采用定点供应,砂采用中砂(MX=3.0-2.3),石料粒径为10mm~25mm。各类材料公司提供质量保证书,并且全部进行取样试验,合格后方能投入生产使用。各类材料严格按品种、规格分类挂牌堆放,不得有混堆、混仓现象。原材料复试规定:
水泥:以同一厂家、同一品种、同一标号、300T为检验批,按GBI75-99规定试验。
砂:以同一产地,600T为检验批,按GB/T14684-2001《建筑用砂》标准进行检验。
石:以同一产地,600T为检验批,按GB/T14685-2001《建筑用卵石、碎石》标准进行检验。
钢筋:按GB13013标准进行复试。
必须根据材料进厂的情况、实验结果做好材料台帐汇总。
2. 生产过程质量控制
2.1 钢筋骨架制作
水泥管生产必需对各道工序进行自检,并填写自检记录。
钢筋制作应严格按设计图纸要求进行加工。如遇变化,必须根据设计变更规定进行。
经常对钢筋加工机械进行保洁、防止钢筋在加工时沾染油污。
每班在生产前或生产过程中对加工的半成品按品种、规格分类挂牌堆放,以防误用。
骨架成型前,应检查钢筋靠模的尺寸,以控制钢筋骨架的几何尺寸误差。
骨架成型后,必须检查是否按图纸施工(包括钢筋的规格、数量、位置是否正确,焊接是否牢固,焊缝的要求是否符合规定)。
按图纸要求对半成品钢筋骨架的几何尺寸(按10%且每班规格不少于一件)、钢筋骨架的外观质量进行专检,不合格品禁止使用,并另行堆放。检查要求及规定见表1、表2。
2.2 拼模及骨架入模
生产班组应将每支水泥管模具中的混凝土残渣全部消除干净。隔离剂采用洁净优质产品,涂刷均匀,不得有积油、淌油、漏刷现象,不得涂刷废机油。模具合拢前,应仔细检查压浆孔、预埋件是否正确到位,焊接是否牢固,骨架是否沾油污,并做好自检记录。
现场质检员应对模具的清理、隔离剂涂刷、压浆孔、预埋件、保护层、垫块情况逐项进行目测,对不合格者进行纠正处置。
2.3 混凝土搅拌及成型
严格按混凝土配合比进行投料,在开拌前由操作工、质检员共同核对配合比及所用各类材料的品种、规格及称量,作好拌和记录。经常做好称量较零工作,在拌和过程中每班对拌和时间、称量误差、维勃度应进行1~3次实测检查,发现异常必须停止搅拌,检查原因并调整后方可继续搅拌。
水泥管悬辊成型,转速应取高速,辊压密实。质检员应按规定要求及时作好混凝土试块。抗压试块每班不少于3组(9块),及时压出上一班起吊强度,合格后通知车间。
计量员应经常检查拌和称量设备器具情况,每月不少于一次称量静态校验,保证称量准确性。
2.4 水泥管的蒸养、脱模及养护
管材采用蒸汽养护,应有专人负责控制蒸养温度,严格按养护制度控制,做好记录。管材的蒸养制度见图1。
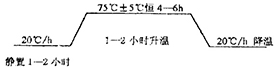
图1 管材的蒸养制度
蒸养完毕,对同条件蒸养试块进行强度检测,达到75%设计强度时通知车间起吊。
2.5 成品出厂检验
水泥管脱模后,应逐件编号(生产日期、型号)并进行外观质量检验;每班不少于10%,每种型号不少于1件进行几何尺寸检验。检验后按合格与不合格品分别盖章堆放。
3. 健全管理制度
3.1 建立上下道工序交接验收制度,在水泥管的生产中,设立工艺流程卡,强化三检制。通过车间的自检、互检及质检科的专检,防止不合格材料或不合格品进入下一道工序。
3.2 确立拌和、装模、悬辊制管为质量控制点,明确管理点的岗位负责人。
人员必须经培训考核,合格后持证上岗。明确管理点的岗位责任制、产品技术标准、操作规程、检测方法及控制、检测频次。
3.3 定期做好机械设备、计量测试设备的维修保养,保证所用设备仪器准确、完好。检验检测仪器和计量工具,严格按国家检定规程送计量部门进行检定。检定合格后方可投入使用。
3.4 加强产品质量考核,按照厂奖罚管理规定实施奖罚。
1. 原材料控制
根据水泥管生产的特殊性,砂、石采用定点供应,砂采用中砂(MX=3.0-2.3),石料粒径为10mm~25mm。各类材料公司提供质量保证书,并且全部进行取样试验,合格后方能投入生产使用。各类材料严格按品种、规格分类挂牌堆放,不得有混堆、混仓现象。原材料复试规定:
水泥:以同一厂家、同一品种、同一标号、300T为检验批,按GBI75-99规定试验。
砂:以同一产地,600T为检验批,按GB/T14684-2001《建筑用砂》标准进行检验。
石:以同一产地,600T为检验批,按GB/T14685-2001《建筑用卵石、碎石》标准进行检验。
钢筋:按GB13013标准进行复试。
必须根据材料进厂的情况、实验结果做好材料台帐汇总。
2. 生产过程质量控制
2.1 钢筋骨架制作
水泥管生产必需对各道工序进行自检,并填写自检记录。
钢筋制作应严格按设计图纸要求进行加工。如遇变化,必须根据设计变更规定进行。
经常对钢筋加工机械进行保洁、防止钢筋在加工时沾染油污。
每班在生产前或生产过程中对加工的半成品按品种、规格分类挂牌堆放,以防误用。
骨架成型前,应检查钢筋靠模的尺寸,以控制钢筋骨架的几何尺寸误差。
骨架成型后,必须检查是否按图纸施工(包括钢筋的规格、数量、位置是否正确,焊接是否牢固,焊缝的要求是否符合规定)。
按图纸要求对半成品钢筋骨架的几何尺寸(按10%且每班规格不少于一件)、钢筋骨架的外观质量进行专检,不合格品禁止使用,并另行堆放。检查要求及规定见表1、表2。
表1 钢筋骨架焊接外观检查要求
要求 | 引用标准 |
不应有咬肉 | 《钢筋焊接及验收规程》JGJ18-96 |
不应有气孔 | 《钢筋焊接及验收规程》JGJ18-96 |
应清除夹渣 | 《钢筋焊接及验收规程》JGJ18-96 |
不应有漏脱焊 | 《钢筋焊接及验收规程》JGJ18-96 |
钢筋外型平直、洁净 | GB50204-2002 |
埋件外型就位正确牢固 | 《钢筋焊接及验收规程》JGJ18-96 |
表2 骨架几何尺寸检查要求
项目 | 尺寸偏差(mm) | 检查方法 |
网片长、宽 | ±5 | 尺量 |
网片间距 | ±10 | 用尺量 |
环向盘长度 | ±10 | 用尺量 |
环向盘间距 | ±5 | 用尺量 |
主盘保护层 | ±5-3 | 用尺量 |
2.2 拼模及骨架入模
生产班组应将每支水泥管模具中的混凝土残渣全部消除干净。隔离剂采用洁净优质产品,涂刷均匀,不得有积油、淌油、漏刷现象,不得涂刷废机油。模具合拢前,应仔细检查压浆孔、预埋件是否正确到位,焊接是否牢固,骨架是否沾油污,并做好自检记录。
现场质检员应对模具的清理、隔离剂涂刷、压浆孔、预埋件、保护层、垫块情况逐项进行目测,对不合格者进行纠正处置。
2.3 混凝土搅拌及成型
严格按混凝土配合比进行投料,在开拌前由操作工、质检员共同核对配合比及所用各类材料的品种、规格及称量,作好拌和记录。经常做好称量较零工作,在拌和过程中每班对拌和时间、称量误差、维勃度应进行1~3次实测检查,发现异常必须停止搅拌,检查原因并调整后方可继续搅拌。
水泥管悬辊成型,转速应取高速,辊压密实。质检员应按规定要求及时作好混凝土试块。抗压试块每班不少于3组(9块),及时压出上一班起吊强度,合格后通知车间。
计量员应经常检查拌和称量设备器具情况,每月不少于一次称量静态校验,保证称量准确性。
2.4 水泥管的蒸养、脱模及养护
管材采用蒸汽养护,应有专人负责控制蒸养温度,严格按养护制度控制,做好记录。管材的蒸养制度见图1。
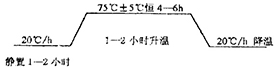
图1 管材的蒸养制度
2.5 成品出厂检验
水泥管脱模后,应逐件编号(生产日期、型号)并进行外观质量检验;每班不少于10%,每种型号不少于1件进行几何尺寸检验。检验后按合格与不合格品分别盖章堆放。
3. 健全管理制度
3.1 建立上下道工序交接验收制度,在水泥管的生产中,设立工艺流程卡,强化三检制。通过车间的自检、互检及质检科的专检,防止不合格材料或不合格品进入下一道工序。
3.2 确立拌和、装模、悬辊制管为质量控制点,明确管理点的岗位负责人。
人员必须经培训考核,合格后持证上岗。明确管理点的岗位责任制、产品技术标准、操作规程、检测方法及控制、检测频次。
3.3 定期做好机械设备、计量测试设备的维修保养,保证所用设备仪器准确、完好。检验检测仪器和计量工具,严格按国家检定规程送计量部门进行检定。检定合格后方可投入使用。
3.4 加强产品质量考核,按照厂奖罚管理规定实施奖罚。